Summary of hazard
Stockpiles and other loose materials are generally loaded onto trucks by front-end loaders. Faceshovels are also used to load blasted or loose materials in pits, quarries and larger stockpiles, and work the stockpile similar to front-end loaders.
At a given height and environmental conditions, stockpile materials will vary in strength and overall stability. They usually remain stable if they rest at their natural slope angle. However, if stockpiles are over steepened or undercut during loading operations, they may slump or collapse, and strike or bury loader operators and other workers and equipment.
There have been several recent incidents on Western Australian mining operations involving the failure of stockpile faces.

Note: A stockpile face is “undercut” when the toe or base is advanced more than the overall face or slope. A face may also be undercut if loaders push materials at the base of the stockpile along, rather than towards, the face. Early warning signs of failure include visible cracking of the crest or top edge of the pile, and small rocks or particles rolling down the face.
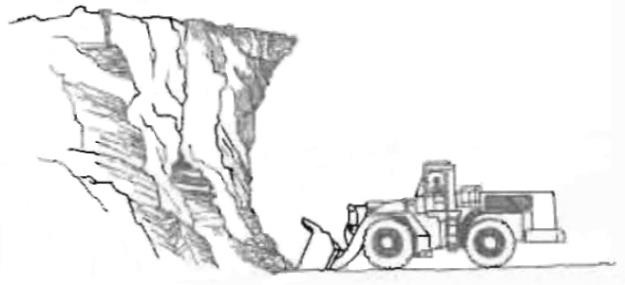
While the design, construction and operation of stockpiles or other loose materials may differ between mines, the groups of workers that may be affected by unstable stockpiles include:
- loader and dozer operators
- supervisors and safety representatives carrying out inspections
- surveyors carrying out measurements or mapping
- geotechnical engineers carrying out inspections
- geologists and grade controllers
- maintenance crews
- other workers who, by the nature of their job, find themselves at or around stockpiles.
Contributory factors
Factors that contribute to the failure of stockpiles include:
- improper design, construction and operation of stockpiles
- inadequate assessment of material properties and environmental conditions, and their influence on stability
- inadequate and inappropriate equipment working on stockpile faces higher than the equipment’s reach
- lack of hazard awareness and insufficient risk assessments that address identified hazards
- inadequate systems of work that expose operators and other employees to hazards
- inadequate supervision and deficient workplace inspections
- inadequate task-specific training.