Background
Batch-type pneumatic filter presses are pressure vessels (i.e. classified plant) commonly found on mine sites in gold rooms, assay laboratories and other metallurgical test facilities. They are typically used to remove the liquid fraction from small batches of mineral slurries to produce a damp filter cake, which is further dried before analysis.
Although designs vary, most units typically consist of a cylindrical barrel supported in a free-standing frame. The top closure is commonly clamped in place using a bridge bar and manually operated power screw (or pneumatic actuator). The bottom closure supports the filter cloth or metal mesh and includes collector channels directed to a filtrate drain nozzle.
Liquid is pressed out of the filter cake using regulated compressed air (typically < 700 kPag), which is fed into the cylinder barrel above the liquid level. The filtrate nozzle is left open to allow the liquid to drain out.
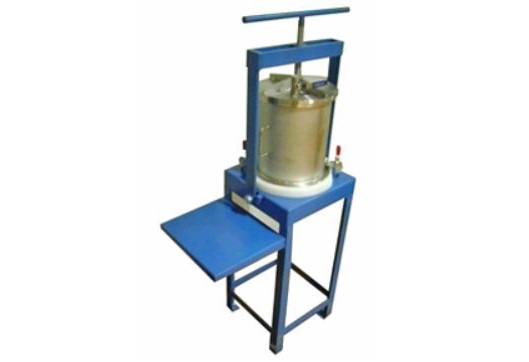
Summary of hazard
Numerous hazards can arise with this type of equipment, including:
- uncontrolled release of pressure, liquid and material (from the seals) while the filter is pressurised
- premature seal failure, with the potential for uncontrolled pressure release and loss of containment if
- seals are not checked for chemical compatibility with the liquid materials being filtered, particularly when tasks change in the laboratory
- there is an uncontrolled substitution of sealing materials with alternatives not approved by the original equipment manufacturer (OEM)
- the common hazards associated with the use of compressed air (e.g. air blast, pressure injection), including the generation of noise as compressed air vents through the drain nozzle when liquid is pressed out of the filter cake
- uncontrolled release of pressure if incorrectly rated hose or fittings are substituted (e.g. water hose instead of air hose) when the compressed air supply connection is not permanently fixed
- unsecured free-standing filter presses being knocked or pulled over
- hazardous manual tasks associated with repeated disassembly, assembly and clamping down of the top and bottom closures (e.g. charging with mineral slurry, removal of filter cake, cleaning and maintenance).
Contributory factors
Since filter presses work with the filtrate drain always open, some duty holders are operating under the misconception that this type of equipment is not categorised as a pressure vessel (i.e. classified plant). However, to slowly force liquid out, the filter barrel necessarily stores pressure above the filter cake for prolonged periods. In addition, pressure will build if the filtrate outlet becomes blocked and the drain valve is inadvertently left closed.
Recent mine site inspections have identified many issues and potential problems with this type of equipment. Factors that may contribute to an increased risk of harm include:
- failure to
- install and maintain an appropriate safety relief device to protect the vessel in situations where the filter press can be inadvertently over-pressurised
- proactively inspect and maintain the equipment, instead of “running to failure”
- secure air hose connections with locking pins, clips or whip checks
- adequately secure the filter to the floor or bench
- provide adequate warning and instruction signs for equipment
- undertaking ad hoc modifications, such as
- substitution of seals
- using incorrectly rated air hoses and fittings
- replacing corroded barrels with pipe sections of different material or wall thickness
- fitting additional leverage on the closure capstan and excessive tightening of the top closure, which can increase the risk of failure and uncontrolled pressure release by overstressing the barrel of the filter or bridge piece, or damaging the seals
- lack of operator awareness of
- the design pressure or maximum allowable working pressure (MAWP) of equipment (e.g. connecting filter presses to 7, 8 or 10 bar compressed air supplies without checking that the filter press is adequately protected from over-pressure)
- the corrosion allowance or need to monitor wall thickness when inspecting and maintaining equipment.