Background
Down-the-hole drill rigs that use reverse circulation (RC) techniques are commonly used for mineral exploration and for sampling purposes in open pit mining. These drill rigs use high pressure (HP) air compressor systems, either mounted on the rig or on a separate compressor truck.
The HP air compressor systems are typically based on oil-flooded rotary screw compressors (OFRSC) for the first stage compression, with a second stage booster compressor and associated intercooler, aftercooler, scrubbers, air-oil separator tank (incorporating a coalescing filter), air receivers and other ancillary equipment.
Numerous potentially serious explosions and fires on drill rigs reported to the Department in recent times have been attributed to issues with the HP compressor on RC drill rigs. Investigation of these incidents suggests that there may be systemic issues with the design, operation and maintenance of this class of equipment, as well as a lack of hazard awareness.
Summary of hazard
Other than general machinery hazards (such as noise, moving parts, hot surfaces, etc.), HP compressor systems on RC rigs have particular hazards and risks.
- Extremely high air pressures (350-500 psi)
- External fires fueled by oil leak
- Internal flash-overs.
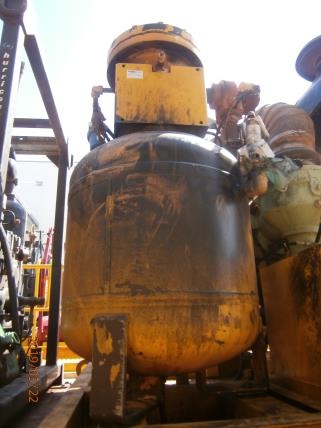
Contributory factors
- High discharge air temperatures increase the risk of fires and explosions. HP compressor systems typically include a discharge air temperature switch that shuts down the machine when the discharge air temperature reaches 110 degrees Celcius, which suggests a problem exists with the compressor or its cooling systems. If the switch is faulty, then the compressor will continue to run and if the discharge air temperature reaches the auto-ignition temperature of the lubricating oil, an internal flash-over event may result.
- Other causes of high discharge air temperatures in a compressor system may include:
- loss of lubricating oil to the compressor screws (e.g. clogging of oil lines, oil filters, valves) because the lubricating oil also cools the air end
- fouled radiators (intercoolers and aftercoolers) not cooling effectively
- radiator cooling fans not working
- dirty or oxidised lubricating oil
- low lubricant levels
- malfunction of oil temperature control valve
- high ambient temperature or lack of ventilation for compressor.
- Excessive oil carry-over past the air/oil separator and any booster inlet scrubbers may increase the risk of fires and explosions. Factors that may increase oil carry-over include:
- sing non-original equipment manufacturer (OEM) approved air/oil separator elements, as well as damaged or wrongly fitted elements
- scubbers and scavenging systems that are not operating effectively
- using the wrong oil grade for the ambient conditions
- using an air/oil separator vessel that is not optimally sized for your air system (e.g. wrong wet side volume).
- Any undrained dead legs in the compressed air piping can become condensate traps and accumulate oily liquid over time. Such accumulations of oil may fuel an internal fire or contribute to a flash-over event.
- Compressed air systems on RC rigs are commonly fitted with spring type safety relief valves, usually mounted on the air/oil separator vessel. Such devices are not designed to relieve the sudden over-pressure produced by a flash-over event.