Background
In July 2020, a service crew at an underground mine was hanging an electrical trailing cable for a jumbo drill in an ore drive, when two workers were tipped out of a work platform (WP) attached to an integrated tool carrier (ITC).
As the two workers were hanging the cable from the WP, a hydraulic failure associated with the tilt cylinder (crowd function) on the boom of the ITC caused the WP to tilt fully forward under gravity. Due to the sudden and unexpected movement, one of the workers was ejected from the WP onto the ground below while the other remained in the WP as his right boot was caught in the door.
The hydraulic failure resulted from the anti-dump valve on the tilt cylinder becoming separated from the cylinder port when its mounting bolts sheared. The mounting bolts sheared when the body of the anti-dump valve clashed with the lifting frame of the ITC as the boom was being raised.
The floor of the WP was reported to be approximately two metres off the ground immediately prior to the incident, and despite both workers wearing fall control equipment, their shock adsorbing lanyards failed to deploy. Although the two workers received minor physical injuries, the potential consequences could have been much more serious.
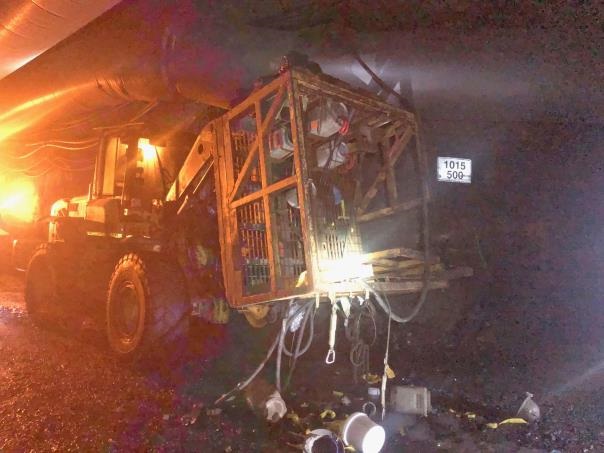
Summary of hazard
For persons working within a WP there is risk of exposure to fall from height hazards due to the following potential causes:
- machine components failing (e.g. WP detaching from quick hitch, dog-bone failure, hydraulic failure)
- machine overturning (e.g. from operating the machine beyond its load and stability limits, uneven ground conditions)
- persons being ejected from the WP due to the "catapult effect" (e.g. wheels contact an obstacle or depression when tramming with persons in the WP)
- machine driving over an edge (e.g. unbunded open stope).
The July 2020 incident was the third in a recent series of serious and potentially serious events relating to WP and ITC combinations used underground at different mine sites. These incidents were:
- March 2018: WP detached from quick hitch and fell to ground – one worker injured
- February 2020: dog-bone failure – two workers injured when they were ejected from an underground WP
- July 2020: anti-dump valve failure – two workers injured when they were ejected from an underground WP.
Contributory factors
In the case of the July 2020 incident, there were a number of key contributory factors involved.
- The anti-dump valve fitted to the tilt cylinder had been retrofitted to the ITC by a previous owner. It was neither a standard nor an optional feature provided by the original equipment manufacturer (OEM), but an after-market retrofit. The OEM manuals available to maintenance personnel contained no information regarding this device or how it should be installed, tested and commissioned.
- The anti-dump valve included no guard or cover to protect it from physical impact. Other ITCs in the same fleet had robust protective covers on their anti-dump valves.
- The anti-dump valve involved in the incident required an adapter block for mounting. The adapter block made the "anti-dump valve" more vulnerable to impacts and allowed mounting in two different orientations. One of the available orientations did not allow clearance for the full range of boom elevation. These issues were not known to maintenance personnel and there were no mounting, testing or commissioning instructions available to them. A correctly sized anti-dump valve should match the hydraulic port size and mounting holes on the hydraulic cylinder so it can be directly mounted.
- After the anti-dump valve had been fitted to the tilt cylinder, the tilt capability was function tested, but the boom lift had not been function tested through the full range of movement. The anti-dump valve only clashed with the lifting frame of the ITC when the boom was raised close to full height during subsequent operational use.
- The WP and ITC combination was functionally a Type 2, Group B vehicle mounted mobile elevating work platform (MEWP). However, it was not fully compliant with AS1418.10:2011 and was not being managed as registered classified plant. Furthermore, because the equipment was essentially being managed as earthmoving equipment rather than as an MEWP, the periodic inspection requirements of AS 2550.1 were not being followed.
- Although both workers were wearing fall arrest harnesses with standard 1.5-metre long shock adsorbing lanyards attached to fall arrest anchor points on the front of the basket, the WP was not being used at sufficient height for the fall prevention system to stop the users from impacting the ground. No inertia reel type devices were used. A combination of shorter lanyards, alternate anchor points and/or inertia reel devices may have provided better protection.