An electrician and mechanical fitter investigating water-overflow issues at an underground mine found that a 90 kW submersible pump supplied from a 415 V motor control centre (MCC) had faulted. The electrician started investigating the pump control cubicle. He identified that a control relay contact had fused in the closed position and a control circuit breaker had tripped. The electrician replaced the control relay for the main contactor and, after examining the cubicle, reset the control circuit breaker.
The electrician closed the cubicle door but without properly securing it. He then switched the main circuit breaker to the “ON” position. At that instant, there was an arc flash and blast, which blew open the door of the cubicle. The electrician received first degree burns to his neck, face and ears, while the fitter received a minor facial injury.
The subsequent investigation revealed that the main circuit breaker had suffered a phase-to-phase arcing fault. The arcing fault started within the main circuit breaker terminal on the line side of the blue phase, and then transferred to a three-phase fault.
Direct causes
- The pump supply cable blue phase was shorted to earth (as confirmed by an insulation resistance test after the incident).
- The electrical circuit was not designed to automatically disconnect the main circuit breaker under an earth leakage or earth fault.
- The protection settings were not coordinated correctly, therefore the upstream air circuit breaker connected to the 415 V MCC busbars failed to operate. The high voltage circuit breaker connected on the primary side of the 750 kVA transformer cleared the arc fault current of about 9.5 kA in more than 1 second.
Contributory causes
- The pump cable was not tested for insulation resistance prior to energising at the cubicle.
- The drawings did not match the electrical installation. Specifically, the trip circuit of the motor overload protection had been bypassed, allowing the pump to operate under overload conditions.
- The pump was designed to automatically start or stop depending on the status of the float switch. As soon as the electrician turned the main circuit breaker to the “ON” position, the high water level in the tank was detected by the float switch and energised the main contactor.
- The inspection and maintenance processes for testing functionality of protective devices were inadequate and had not detected the issue with the protection settings not being coordinated.
- The cubicle door was not secured correctly prior to switching on the main circuit breaker.
- The potential for arc flashing was not identified and the workers were not wearing adequate facial protection.
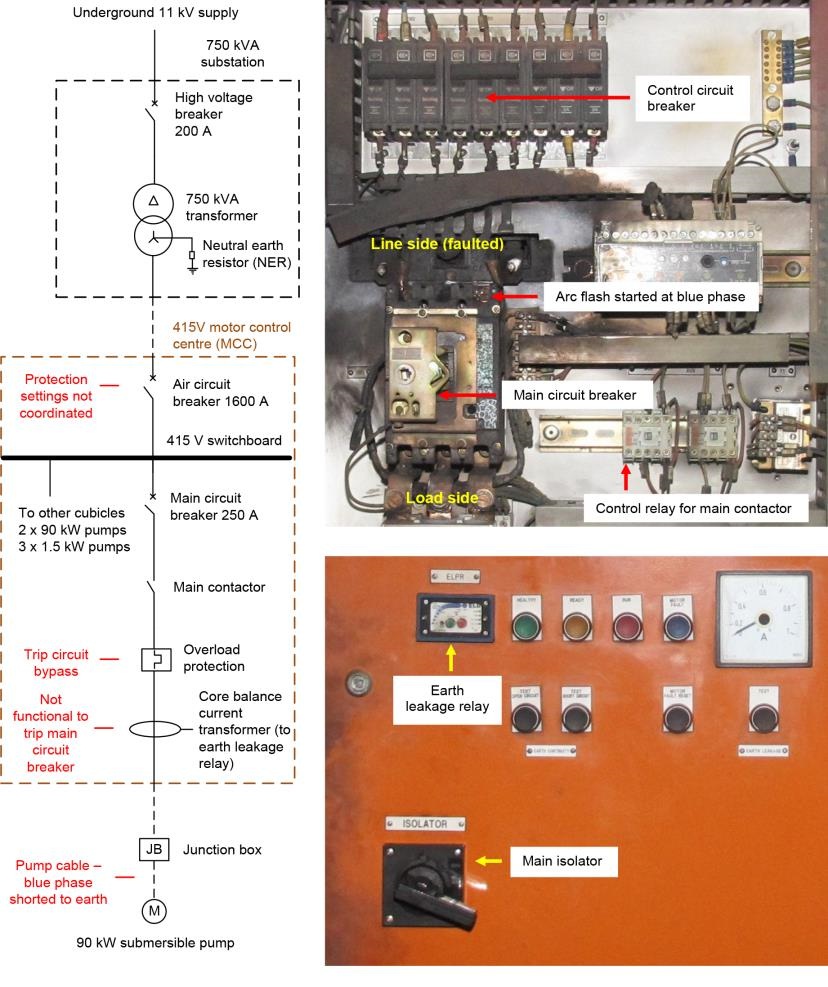