Summary of incident
In August 2016, two shotfirers were attempting to initiate an open pit blast with a remote firing device (RFD). After two failed attempts, it was decided to manually fire the shot using a stomper (manual initiation device).
The shotfirers rolled out detonating cord from the blast site to the firing position on the waste dump, located outside the blast exclusion zone. A long-period delay detonator (LP detonator; 3.6 m lead, 9.6 sec) was connected to the stomper.
On the first attempt the stomper’s shot-shell failed. On the second attempt the shot-shell fired, but when the detonator did not fire instantly one of the shotfirers thought the detonator had failed. The shotfirer cut the detonating cord below the detonator and picked up the detonator (and attached cord) to discard it. At this point the shotfirer realised it was a LP detonator and dropped it – a few seconds before it fired, initiating the attached detonating cord.
Without reporting the incident to the quarry manager, the blast crew proceeded to fire the shot manually after sunset, with a new LP detonator. Fortunately, there were no serious injuries or fatalities.
Direct causes
- Poor practice in the use of the manual initiation device (stomper) which was connected to a LP detonator rather than a lead-in line (signal tube) of sufficient length.
- The shotfirers were in a position where they were exposed to an explosives hazard (i.e. detonator and detonating cord initiating the shot).
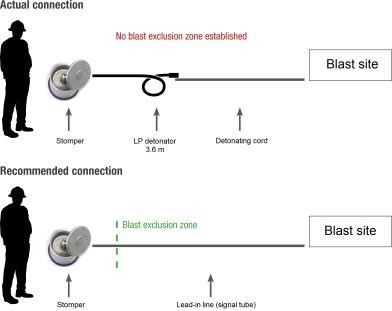
Contributory causes
Safe systems of work
- The formal risk management processes failed to identify deficiencies in risk controls for the use of explosives on site.
- There was no procedure, formal training or assessment on the correct use and application of the stomper.
- Inadequate supervision and monitoring practices contributed to the failure to identify a procedural gap in the use of the stomper.
- The risks associated with the change in work plan were not assessed using the site’s taskbased risk assessment tool.
Blasting practices and equipment
- LP detonators were not fit-for-purpose and were being used to run down excess stock.
- The blast plan design and document approval process was flawed (e.g. hook-up details were insufficient, hazards associated with use of LP detonators were not recognised).
- The primary initiation system for the shot failed.
Note: Problems with the remote firing device had been experienced in previous blasts. However, these were not rectified. - The blast crew felt under pressure to fire the shot due to conditions (fading light, rising water levels) and to meet production requirements.