Summary of incident
In December 2016, a cone crusher became bogged following a power outage, requiring the lifting of the crusher bowl (via the spring packs) to clear the blockage. To achieve this a hydraulic ram (lifting jack), with two steel packing plates placed beneath its base, was positioned on the countershaft ledge. Another steel packing plate was placed between the extension arm of the ram and the retaining plate of the spring pack above.
While a fitter was using a flogging spanner to release tension on a nut under the spring pack in front of him, a packing plate beneath the ram dislodged under pressure. The fitter, who was straddling the crusher’s countershaft took the full-force of the plate to his sternum, receiving a significant chest injury.
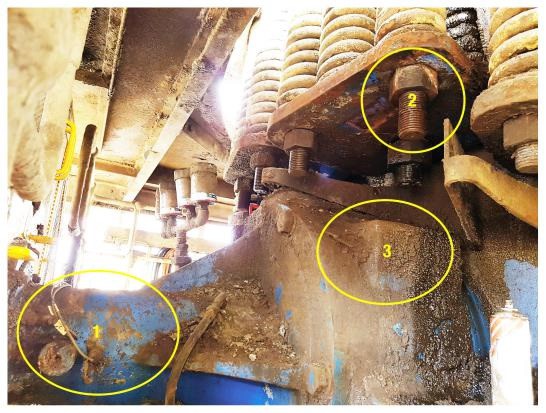
Note: The cone crusher's internal hydraulic clearing system had been inoperable for over twelve months. At the time of the incident, seven of the twelve hydraulic cylinders were leaking. Repair of the leaking cylinders was planned for a November 2016 shutdown, but due to a delay in receiving parts, did not happen.
Direct causes
- The fitter was in the line-of-fire of the steel packing plate when it dislodged under pressure.
- The lifting of the crusher bowl was conducted manually.
Contributory causes
Incorrect hydraulic jacking method
- The countershaft ledge on which the hydraulic ram was positioned was covered in mud and oil, not level and installed out of alignment with the spring pack.
Note: The countershaft ledge was not identified in the original design drawings and is considered a modification. - The steel packing plates were contaminated by oil (reducing the friction on the packing plate surface) and positioned offset to the hydraulic ram, increasing the potential for release during equipment movements.
Safe systems of work
- The hazards posed by the long-term inoperability of the hydraulic clearing system and the offset countershaft ledge were not effectively identified, evaluated or adequately addressed.
- There was no safe system of work for jacking activities.
- The job hazard analysis (JHA) developed for the task failed to recognise the potential for the release of stored energy and workers being in the line-of-fire.